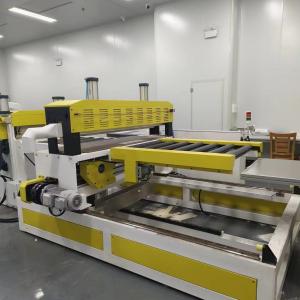
Add to Cart
A sheet extruder is a piece of equipment used to produce plastic sheets. It forms molten plastic into a continuous sheet-like product by heating, melting, and pressure pushing plastic pellets or pellet mixtures through an extrusion die.
1. Flat and uniform: After the sheet extruder melts the plastic through the extrusion process, the molten plastic is formed into a flat sheet through the extrusion die. These sheets have relatively uniform thickness and surface quality, which can meet the packaging industry's requirements for appearance.
2. Strong customizability: The sheet extruder can adjust the configuration and parameters of the extruder according to the needs to produce various plastic sheets. The extrusion speed, extrusion temperature, mold design, etc. of the extruder can be adjusted to meet the requirements of different materials, sizes and shapes.
3. Stable physical properties: The plastic sheet produced by the sheet extruder has stable physical properties, such as strength, toughness, wear resistance, etc. These properties can be adjusted according to the selected plastic material and extrusion process to meet the requirements of the packaging industry for material properties.
4. Various types of materials: sheet extruder can process many different plastic materials, such as polyethylene, polypropylene, polyvinyl chloride, etc. This enables the extruder to meet the needs of the packaging industry for different material properties such as chemical resistance, heat resistance, transparency, etc.
5. Recyclable: Most of the plastic sheets produced by the sheet extruder can be recycled and reused. This helps reduce waste generation and promotes the development of sustainable packaging.
In general, the plastic sheet produced by the sheet extruder has the characteristics of flatness and uniformity, strong customizability, stable physical properties, various types of materials, and recyclability. These features make the sheet extruder widely used in the packaging industry and meet the requirements of different packaging needs.
Items | Parameters |
---|---|
Screw Design | Customized |
Cooling System | Water |
Control System | PLC |
Extrusion Head | Customized |
Material | Plastic |
Extrusion Speed | High |
Screw Length | 33:1 |
Power Supply | 220V/380V |
Drive System | Servo |
Extrusion Capacity | High |
application:
Plastic extruders are an indispensable part of modern industry. Widely used in various fields such as food, medicine, packaging, construction, etc., it has the advantages of high efficiency, long service life, and low energy consumption. The brand is Chundi, and the model is 120mm. It is made in China and its heating system is electric. Its extrusion method is continuous, its extrusion head and die are customized, and its screw design is also customized. Ideal for extruding plastic materials such as PET sheets. Twin-screw extruders are designed to provide a reliable and stable extrusion process.
Plastic extruders are widely used in various industries such as plastic film production, pipe extrusion, injection molding, and cable insulation. They are suitable for producing plastic products of various shapes, such as films, sheets, pipes, profiles, and the extrusion process is reliable and efficient. . Extruder plastic machines can also be used to produce PET sheets. Twin-screw extruders are designed to provide a stable and reliable extrusion process for the production of PET sheets. Extruder machinery is easy to operate and maintain. It is a reliable and cost-effective solution for plastic extrusion.
Plastic extruders are ideal for producing plastic products with high precision and superior performance. It is a reliable and cost-effective choice for various industries. Extrusion heads and dies can be customized to meet specific requirements. The screw design is also customized to ensure high efficiency and stability. Twin-screw extruders are designed to provide a reliable and stable extrusion process for the production of PET sheets and other plastic materials.
We offer technical support and service for Plastic Extrusion Machine. Our team of experts provides on-site consultation and maintenance, as well as remote technical support. We offer training sessions for new and existing customers, and can help with installation and product customisation. We also provide spare parts and repair services for Plastic Extrusion Machines.